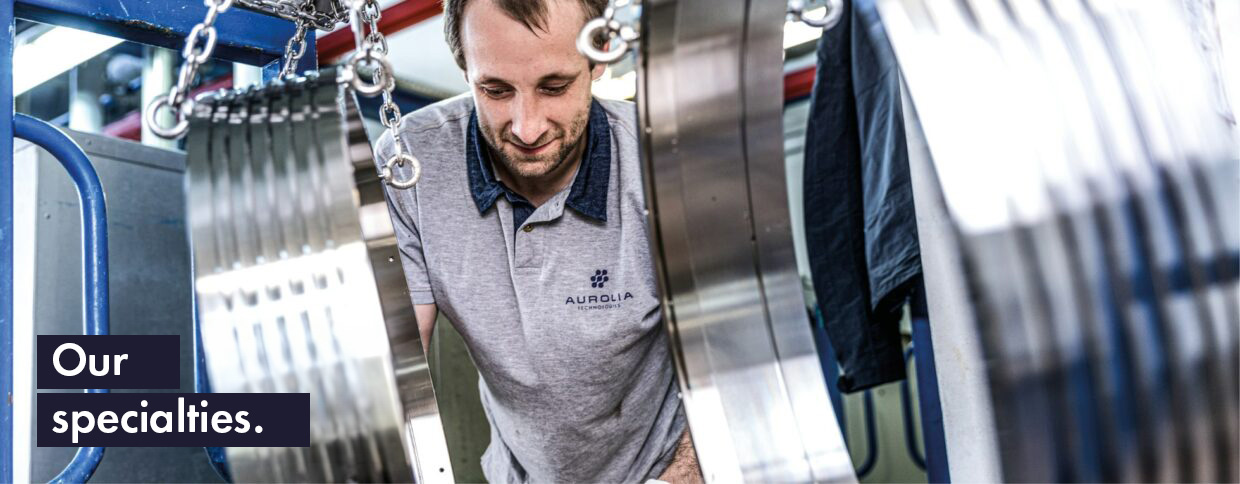
Proceedings
Three paths to the perfect surface
To achieve a perfect surface, Aurolia primarily utilizes three electroplating processes. With their assistance, we can positively influence many important properties of the material. Aurolia surfaces are harder, more durable, more wear-resistant, and corrosion-resistant. Our customers specify the requirements, and we create a surface layer that precisely meets their needs, from functionality to texture and appearance.
Overview of our processes
Chemical Nickel

Chemical Nickel black

Chemical Nickel Plating
Description
Steel, stainless steel, cast iron, non-ferrous metals, and aluminum: Thanks to various pretreatment measures, many materials can be chemically nickel-plated. Through coating, we significantly enhance corrosion protection and achieve high wear resistance with values of up to 1000 HV. Magnetic insulation properties are also possible. Of course, we can also meet aesthetic requirements. Thus, everything from matte through glass bead blasting to high gloss is possible. By adding additional components, other optical characteristics can also be achieved within certain limits. Our electrolytes work so precisely that even tightly tolerated fits with the coatings are precisely achieved.
We offer chemical nickel in low, medium, and high phosphorus ranges, in black, PTFE, or dispersed with boron nitride. As your competent partner, we are happy to assist you with any questions regarding chemical nickel. We work closely with process developers to provide you with practical solutions and the latest developments in high-performance surface technology. We process your components according to DIN EN ISO 4527.
Hard facts
- Chemical Nickel Process
- Processing: Batch and rack coating
- Functional surface for corrosion and wear protection indoors and outdoors
- Texture and appearance dependent on pretreatment (blasted/polished)
- Tight tolerances +/- 2 μm
- Wide range from low to high phosphorus content, from glossy to matte, from sliding to black
- Layers can be combined, e.g., high phosphorus layer on low to increase corrosion protection, and vice versa to increase wear protection
- RoHS, ELV, and FDA compliant
- High chemical resistance
- Low friction coefficient
- Solderable
We are happy to conduct a sampling.
FAQ Chemical nickel plating
What is chemical nickel plating?
Chemical nickel plating is an autocatalytic process in which a nickel layer is applied to a workpiece without an external power source. The nickel deposition takes place through a chemical reaction in a special nickel electrolyte.
What are the advantages of chemical nickel plating?
Chemical nickel plating offers numerous advantages, including:
- High corrosion resistance
- Good wear resistance
- Precise layer thickness
- Uniform layer distribution, even on complex geometries
- Improved surface hardness
For which applications is chemical nickel plating suitable?
Chemically nickel-plated surfaces are often used in the automotive industry, mechanical engineering, electronics, aerospace, as well as in the food and medical technology sectors. The coating is ideal for components that require a uniform protective layer and high corrosion resistance.
How thick is the layer in chemical nickel plating?
The layer thickness can vary depending on the requirements and application, typically ranging between 5 and 50 micrometers. However, thinner or thicker layers can also be applied, depending on the desired protective effect.
What is the difference between chemical and electroplated nickel plating?
In electroplated nickel plating, nickel deposition is achieved using an electrical power source, whereas chemical nickel plating relies on a chemical reaction. Chemical nickel plating enables uniform coating even in hard-to-reach areas, which is more challenging with the electroplating process.
Can chemical nickel plating also be applied to aluminum?
Yes, chemical nickel plating can be applied to various base materials such as aluminum, steel, copper, brass, and other alloys. For aluminum, a special pretreatment is often required to ensure good adhesion of the nickel layer.
Is chemical nickel plating environmentally friendly?
The process uses chemical substances, which is why strict environmental regulations and safety measures are necessary for chemical nickel plating. However, modern processes and systems are efficient in minimizing chemical consumption and ensuring environmentally friendly waste disposal.
Which surfaces can be chemically nickel-plated?
Almost all metallic surfaces can be chemically nickel-plated, ranging from simple machine parts to precise components in electronics. The surface to be coated must be thoroughly cleaned to ensure optimal adhesion of the nickel layer.
How long does the chemical nickel plating process take?
The duration of the chemical nickel plating process depends on the desired layer thickness and the size of the components. Smaller parts can be coated within a few hours, while complex or large-scale components may require more time.
How is the layer quality in chemical nickel plating tested?
Can chemically nickel-plated surfaces be reworked afterward?
Yes, chemically nickel-plated surfaces can be reworked afterward, for example, by grinding or polishing to achieve a specific surface roughness. However, post-processing should be done carefully to avoid damaging the protective layer.
How long does a chemically nickel-plated layer last?
The durability of a chemically nickel-plated layer depends on the application and environmental conditions. In corrosive environments, the coating can last for decades, while it may wear out more quickly under mechanical stress. Regular inspections and, if necessary, recoating can extend its lifespan.