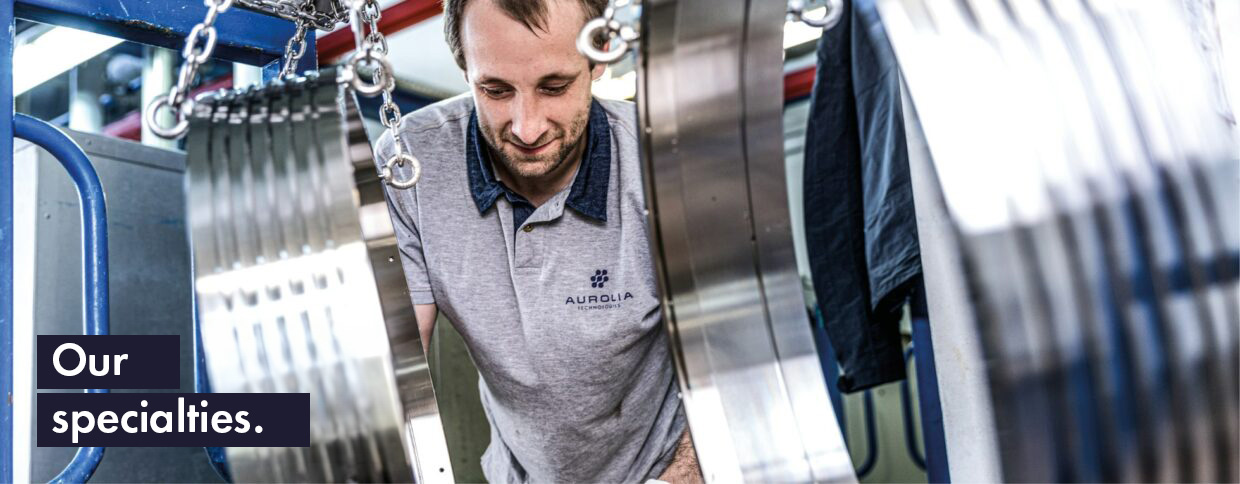
Proceedings
Three paths to the perfect surface
To achieve a perfect surface, Aurolia primarily utilizes three electroplating processes. With their assistance, we can positively influence many important properties of the material. Aurolia surfaces are harder, more durable, more wear-resistant, and corrosion-resistant. Our customers specify the requirements, and we create a surface layer that precisely meets their needs, from functionality to texture and appearance.
Overview of our processes
Anodized black
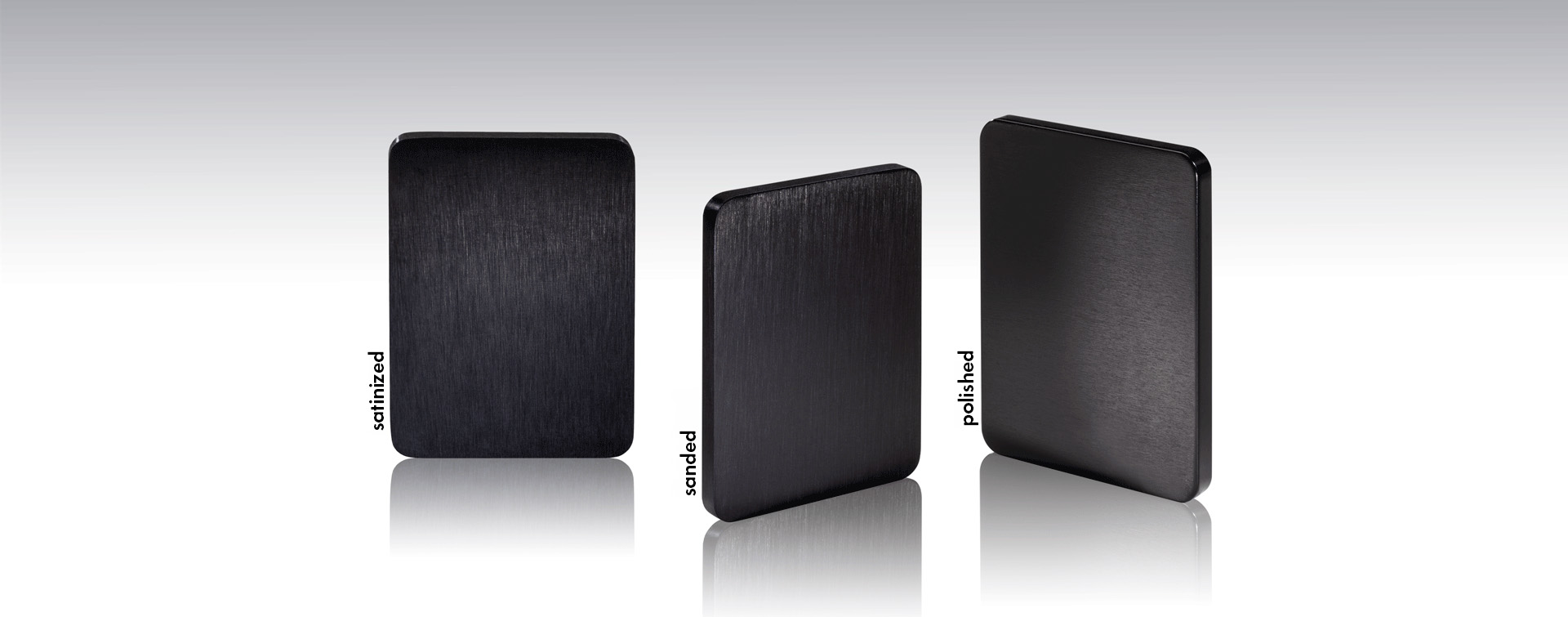
Anodized natural matte etching
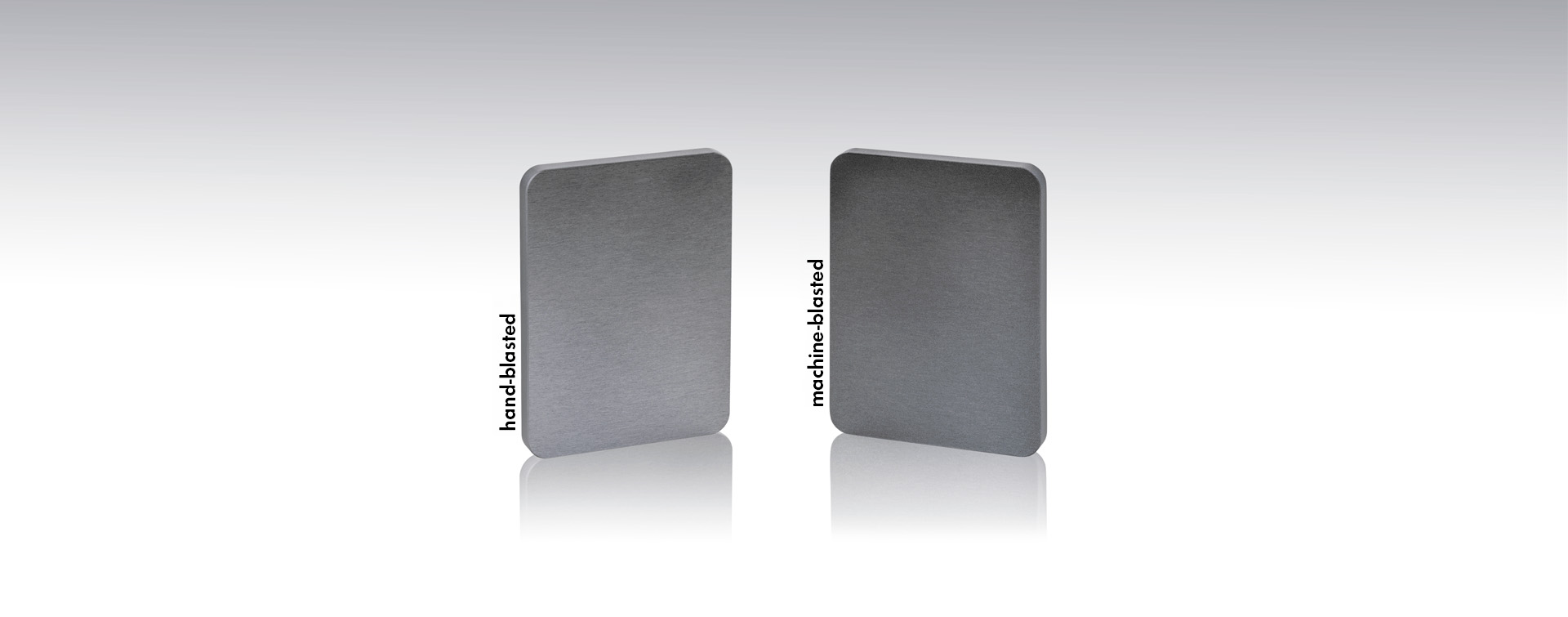
Anodized black decorative etching
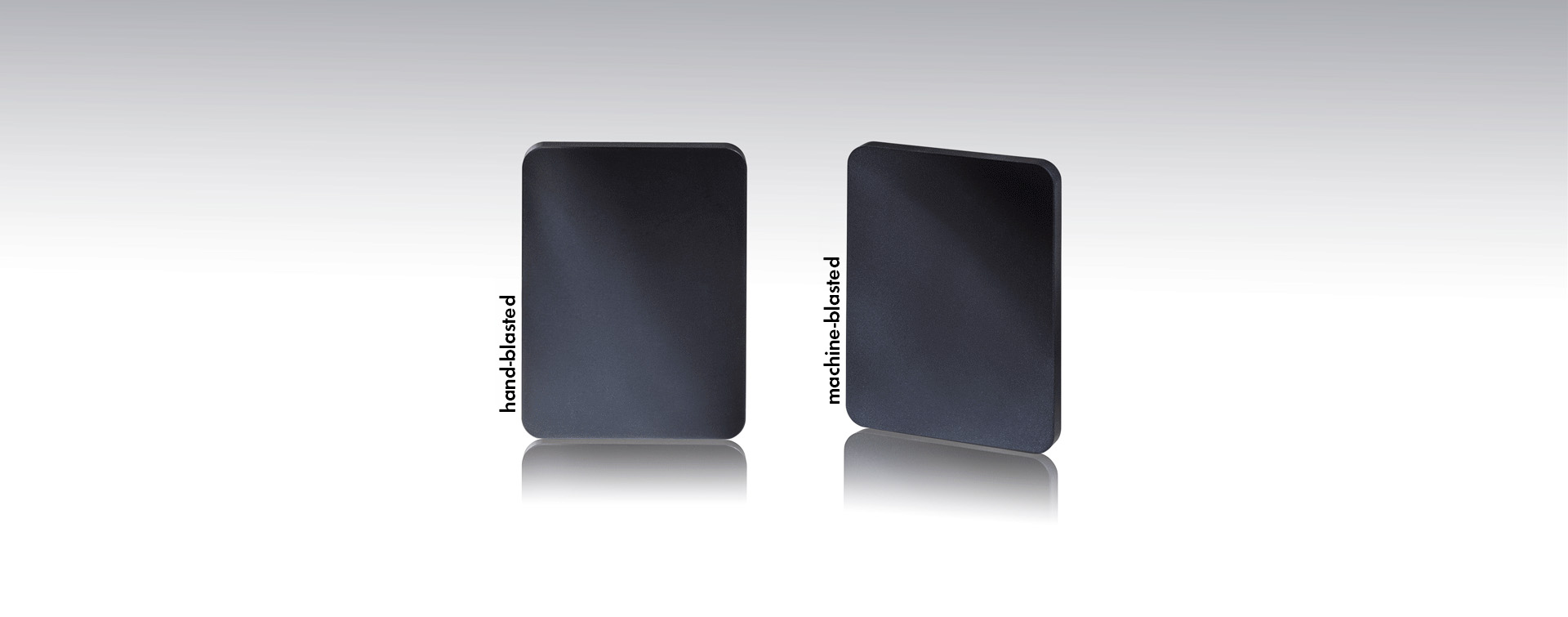
Anodized natural
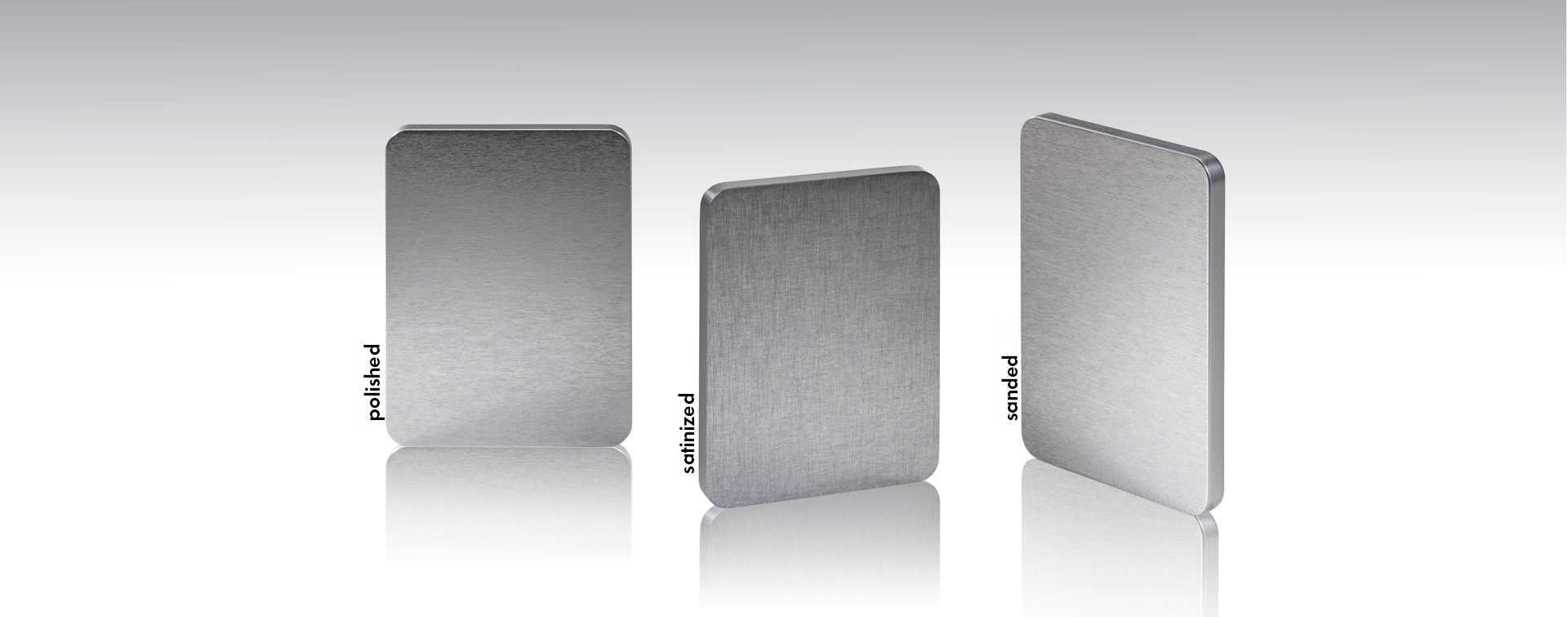
Anodizing
Description
Anodizing provides aluminum with an oxide layer, protecting it from corrosion. This process also occurs naturally, but we manipulate it intentionally to achieve various beneficial properties. We create a layer thousands of times thicker than in nature, three times as hard, with a luxurious texture and appearance. Whether high-gloss, matte, low reflection, stainless steel appearance, or targeted concealment of surface defects, through various processing steps, we enable a wide range of appearances and colors. And thanks to the PLC control of our coating system, we can quickly and accurately reproduce any surface result.
Hard facts
We offer you the following advantages in a work window of 1200 x 700 x 300 mm:
- Decorative mechanical pretreatment
- Tailored coating processes
- Etching as desired
- Coating thicknesses from 5-25 µm
- Coloring according to your preferences
- Good corrosion protection
- Two-stage sealing process
- Good hardness of approximately 200 HV
We are happy to conduct a sampling.
Innovative Anodizing Techniques for the Highest Demands
Anodizing, also known as electrolytic oxidation (Eloxal), is a crucial process that makes aluminum surfaces durable and long-lasting. Particularly when applying black anodizing, not only is excellent corrosion protection ensured, but also an aesthetically pleasing surface that is simultaneously highly functional. This technique is ideal for projects where design and durability are equally important.
Our company offers customized solutions in the field of anodizing, ranging from glossy surfaces to matte and low-reflection variants, and even unique stainless steel looks. Thanks to cutting-edge technology and precise PLC control, we guarantee consistent results and top-quality finishes.
Our black anodized surfaces are especially popular as they offer a luxurious, deep black color that is both robust and scratch-resistant.
For demanding applications, we offer coating thicknesses from 5-25 µm, which can be selected according to specific needs and requirements. The additional ability to dye aluminum surfaces in various colors allows us to meet individual customer desires with precision.
Discover the versatile applications and outstanding benefits of anodizing and let our expertise convince you.
FAQ Anodizing
What is Eloxal?
Anodizing, also known as aluminum anodization, is an electrolytic process used to refine aluminum surfaces. During this process, aluminum is submerged in an acidic electrolyte bath and an electrical voltage is applied. This results in the formation of a protective oxide layer on the aluminum surface. The term "Eloxal" stands for "electrolytic oxidation of aluminum."
This oxide layer created through anodizing is extremely durable and protects the material against corrosion and mechanical wear. Additionally, it can be dyed according to requirements, making the anodizing process particularly attractive for decorative purposes.
Anodizing is therefore a popular choice in various industries, such as automotive, construction, and electronics. Treated aluminum components are not only more durable but also visually appealing. The process preserves the precise dimensions of the workpieces, making it particularly suitable for components that require high dimensional accuracy and surface quality.
Thus, anodizing provides not only protection but also numerous design possibilities for aluminum surfaces.
What is the difference between Eloxal and Eloxieren?
The terms Eloxal and Eloxieren are often used interchangeably, but there is a subtle difference.
Eloxal (short for "electrolytic oxidation of aluminum") refers to the result of the process—that is, the protective and refined oxide layer that forms on the surface of aluminum. This layer offers protection against corrosion, wear, and mechanical stress, and it can also be aesthetically enhanced through coloring.
Eloxieren, on the other hand, describes the process itself—the method by which the aluminum surface is treated in an electrolyte bath under electrical voltage to produce the Eloxal layer. It involves an electrochemical reaction that forms aluminum oxide on the surface, thereby increasing the material's durability.
In summary: Eloxieren is the process, and Eloxal is the result. The two terms are closely connected, as Eloxieren creates the Eloxal layer that protects and enhances the aluminum.
What are the advantages of Eloxal as a surface treatment?
Eloxal, the oxide layer produced through anodizing, offers a wide range of benefits. Here is a concise summary of the key aspects:
1. Corrosion protection:
Eloxal forms a robust protective layer that shields aluminum from moisture, air, and chemicals, making it especially durable and ideal for outdoor applications.
2. Abrasion resistance:
The hard oxide layer is extremely resistant to mechanical stress such as scratches, impacts, and wear, thereby extending the material's lifespan.
3. Decorative design:
Anodized surfaces can be colored in various shades, opening up numerous design possibilities. These colors are long-lasting and fade-resistant, making them particularly valued in architecture and product design.
4. Heat and light resistance:
The layers are resistant to heat and UV radiation, ensuring stability and colorfastness even in challenging environments, such as outdoor areas or high-temperature settings.
5. Dimensional stability:
The oxide layer is tightly bonded to the aluminum without altering the dimensions of the components. This is crucial for precise applications where exact fitting is necessary.
6. Environmental friendliness:
The process does not release harmful chemicals, and treated aluminum remains fully recyclable, making Eloxal a sustainable choice.
7. Easy to clean:
The smooth, dirt-repellent surface is easy to maintain and hygienic, making it ideal for use in kitchens, the food industry, or everyday life.
8. Electrical insulation:
The non-conductive oxide layer can be beneficial in applications requiring electrical insulation, such as in the electronics industry.
Conclusion:
Eloxal combines protection, durability, and design flexibility. These qualities make it a popular choice for aluminum surfaces in architecture, the automotive industry, electronics, and many other fields.
What are the applications for anodized surfaces?
Anodized surfaces offer a wide range of applications due to their functional and aesthetic advantages. Below are some of the most common uses for anodized aluminum:
1. Automotive Industry:
Anodized aluminum parts are widely used in the automotive sector for components such as wheels, body parts, trim strips, and roof racks. The anodized surface protects these parts from corrosion while providing a premium appearance.
2. Aerospace Industry:
In aerospace, anodized aluminum is valued for its lightweight properties, high strength, and corrosion resistance. Common applications include structural components, panels, and electronic housings.
3. Construction Industry:
Anodized aluminum profiles and sheets are extensively used in construction for façades, window frames, doors, and claddings. These surfaces not only protect against environmental influences but can also be aesthetically tailored.
4. Electronics and Electrical Engineering:
In electronics, anodized aluminum is used for housings, heat sinks, and other components. The anodized layer provides electrical insulation, which is advantageous in electrical engineering applications.
5. Furniture and Interior Design:
Anodized aluminum surfaces are used in furniture and interior design for items such as designer furniture, handrails, door handles, and decorative elements. These surfaces are scratch-resistant and can be produced in various colors to meet modern design standards.
6. Medical Technology:
In the medical field, anodized surfaces are frequently used for surgical instruments and medical devices. They are hygienic, easy to clean, and resistant to disinfectants.
7. Household Appliances:
Many household appliances, such as toasters, coffee machines, blenders, or range hoods, feature anodized aluminum surfaces. These are not only visually appealing but also resistant to fingerprints, scratches, and wear.
8. Sports and Recreational Equipment:
Anodized aluminum is used in bicycles, outdoor equipment, tents, and sports gear such as fishing rods and golf clubs. It offers corrosion protection while remaining lightweight and durable, ideal for mobile applications.
9. Architecture and Design:
In modern architecture and product design, anodized aluminum is prized for its elegant appearance and the ability to produce it in a variety of colors. Applications include lighting fixtures, decorative objects, wall claddings, and sculptures.
10. Packaging Industry:
Anodized aluminum is also used in the packaging industry, especially for luxury or technical packaging. The layer protects the material while providing a high-end look.
Conclusion:
Anodized surfaces are used across numerous industries because they combine aesthetic and functional qualities. Thanks to their durability, versatile design options, and corrosion resistance, anodized aluminum is a popular choice for applications requiring long-lasting and high-quality surfaces.
How can I maintain and clean anodized products?
Anodized surfaces are durable and resistant, but regular maintenance and gentle cleaning can extend their lifespan and preserve their appearance. Here are some tips for caring for and cleaning anodized products:
1. Regular Wiping
- Dust and dirt: Use a soft, dry cloth or microfiber cloth to regularly remove dust and dirt from the surface. This prevents scratches caused by dirt particles.
- Light soiling: A damp cloth with warm water is often sufficient to wipe away light dirt. If necessary, add a small amount of mild dish soap.
2. Avoid Harsh Cleaners
- No abrasive cleaners: Avoid abrasive cleaning agents or scrubbing pads, as they can scratch or damage the anodized surface.
- No strong chemicals: Do not use strong alkaline or acidic cleaners, such as descalers or aggressive degreasers, as they may damage the protective layer and dull the surface.
3. Use Mild Cleaners
- Gentle detergents: Use mild cleaning agents designed for aluminum. A pH-neutral cleaner or a gentle all-purpose cleaner is a good choice.
- Avoid solvents: Chemical solvents like acetone, turpentine, or alcohol should not be used, as they can damage the anodized surface.
4. Removing Stubborn Stains
- Warm water and soap: For tougher stains, use warm water with some dish soap and a soft sponge or cloth.
- Special cleaning agents: For particularly stubborn dirt, such as grease stains, use special aluminum cleaners. Ensure they are suitable for anodized surfaces.
5. Prevent Scratches
- Soft materials: Always use soft cloths or sponges for cleaning. Scrubbing with rough materials can scratch the anodized surface.
- Surface protection: For heavily used or exposed areas, consider using additional protective films or covers to prevent scratches.
6. Regular Maintenance
- Care products for anodized aluminum: Apply special care products to protect the surface and maintain its shine. These products are specifically designed for anodized surfaces.
- Refresh the seal: If the seal wears off over time, it can be renewed with special care products to improve water and dirt repellency.
7. Prevent Water Stains
- Dry after cleaning: To prevent water stains, wipe the anodized surface with a dry cloth after cleaning.
- Avoid limescale buildup: Do not let water sit on the anodized surface, especially in areas with hard water, as this can lead to limescale stains.
8. Protection Against Weathering
- Outdoor use: Anodized products used outdoors, such as window frames or façade components, should be cleaned regularly to minimize the effects of weathering. Annual cleaning helps remove dirt and prevent oxidation.
- Corrosion protection: Although anodized surfaces are naturally corrosion-resistant, inspect for damage regularly and address any issues promptly to ensure a long lifespan.
Are there different colors and surface textures for anodized products?
Yes, anodized products offer a wide range of colors and surface textures that can be tailored to various applications and design preferences. Anodizing is not only a functional process to enhance aluminum's durability but also provides numerous aesthetic customization options.
1. Colors of Anodized Surfaces
Anodized aluminum can be colored by introducing pigments into the porous oxide layer during or after the anodizing process. Common colors and methods include:
- Natural Colors (Silver/Gray): Uncolored anodized aluminum retains its natural silver or gray appearance. This is the most common option, offering a simple and timeless look.
- Black: Black anodizing is a popular choice, providing an elegant and modern appearance. It is widely used in the automotive industry, electronics, and architecture.
- Gold: Gold-colored anodized aluminum is often used in decorative applications or in the jewelry and luxury industries.
- Bronze and Brown: These tones are frequently utilized in construction or design objects to create a warm and natural aesthetic.
- Special Colors: Nearly any color is possible, including red, blue, green, and violet. These vibrant hues are often seen in design products, furniture, sports equipment, and electronic housings.
2. Surface Textures of Anodized Products
In addition to various color options, anodized surfaces can be created with different textures, adding both aesthetic and functional dimensions:
- Matte: Mechanical pre-treatments like brushing or sandblasting give the aluminum a matte texture. Matte surfaces are more resistant to fingerprints and scratches, providing an elegant, understated look.
- Glossy: Polishing anodized aluminum creates a mirror-like, reflective surface. Glossy finishes are ideal for decorative applications that demand a high-end, luxurious appearance.
- Textured: Mechanical processing such as ribbing or embossing can be performed before anodizing to produce unique surface textures. These finishes offer a distinctive tactile quality and improved slip resistance.
- Brushed: Brushing aluminum before anodizing results in a uniform, linear texture often seen in electronics and design products. This finish imparts a modern, technical look.
- Perforated: In architectural applications, anodized aluminum sheets are sometimes perforated or stamped. The anodized layer reliably protects even these intricate designs from corrosion.
3. Combining Color and Texture
The possibilities for combining colors and surface textures are nearly limitless. Anodized aluminum can be customized through special pre-treatments (e.g., polishing or brushing) paired with a chosen color. This allows anodized surfaces to be tailored to specific design requirements, from subtle, functional finishes to striking, glossy designs.
4. Weather Resistance of Colors and Textures
One significant advantage of anodized coloring is its UV resistance. Anodized colors do not fade, making them ideal for outdoor use. The anodized layer not only protects against mechanical damage but also environmental factors, ensuring that the colors and textures retain their aesthetic quality for a long time.
Conclusion:
Anodized surfaces offer a wide variety of colors and textures. Whether matte, glossy, textured, or brushed, anodized aluminum can be customized to meet both functional and decorative requirements. With its durability and coloring options, anodized products are highly valued in many industries, from architecture to electronics.
Which metals can be anodized?
Anodizing is primarily suitable for certain metals that can form a robust, oxidized protective layer through the process. Here are the metals that can be anodized:
1. Aluminum:
The most common material for anodizing. Aluminum's oxide layer is highly resistant to corrosion and is used in both technical and decorative applications.
2. Titanium:
Titanium can be anodized to produce various colors. This is commonly used in medical technology and jewelry manufacturing due to its biocompatibility and aesthetic appeal.
3. Magnesium:
Magnesium can be anodized, although the process is technically more challenging, and the durability of the oxide layer is generally lower compared to aluminum.
4. Zinc:
Zinc can be anodized for specialized applications. However, its use is limited because the protective properties and durability of the oxide layer are less effective than those of aluminum.
5. Zirconium:
Less common but also anodizable. Zirconium is mainly used in industrial applications, as the anodized layer provides a particularly hard and heat-resistant surface.
Conclusion:
While other metals can be anodized, **aluminum remains the preferred choice** due to its optimal combination of ease of processing, durability, and surface versatility. This makes aluminum the go-to material for a wide range of anodizing applications.
Why is aluminum particularly suitable for anodizing?
Aluminum is the preferred material for anodizing because it naturally forms a thin, protective oxide layer that can be significantly enhanced through the anodizing process. During anodizing, this oxide layer is transformed into a uniform, porous, and extremely durable coating via an electrochemical process. This layer provides excellent corrosion resistance, is abrasion-resistant, and significantly improves the longevity of the material.
Key Advantages of Aluminum for Anodizing:
- Corrosion Resistance: The anodized layer provides exceptional protection against environmental factors such as moisture and chemicals, making aluminum highly durable.
- Color Customization: The porous oxide layer can be infused with dyes, allowing for a wide range of colors. These colors are UV-resistant and do not fade over time, as they are an integral part of the oxide layer.
- Retention of Metallic Properties: Anodizing preserves the natural metallic structure and thermal conductivity of aluminum, making it both functional and visually appealing.
- Lightweight and Strong: Aluminum's low weight combined with the enhanced surface hardness after anodizing makes it ideal for applications requiring strength and reduced weight.
- Eco-Friendly: Anodized aluminum is fully recyclable and the anodizing process is more environmentally friendly compared to other surface treatments.
Applications:
These qualities make aluminum widely used in industries such as architecture, automotive, electronics, and household appliances, where a combination of technical performance and aesthetic appeal is essential.
Conclusion:
Aluminum is perfectly suited for anodizing because it is lightweight, corrosion-resistant, durable, and versatile in appearance—ideal for applications requiring both functionality and attractive design.
What does anodizing aluminum mean?
Anodizing is an electrochemical process that enhances the natural oxide layer on aluminum. This process makes the surface harder, more resistant to corrosion, and scratch-resistant. Additionally, aluminum can be anodized in various colors, offering both functional and decorative benefits.
How does the anodizing process work?
The anodizing process, or the electrolytic oxidation of aluminum, is a precise method that creates a protective oxide layer on the material's surface. During this process, aluminum is immersed in an electrolyte bath, often containing sulfuric acid, and connected to a power source. The aluminum acts as the anode, leading to its oxidation and the formation of a hard, durable layer of aluminum oxide (anodized coating) on its surface.
Steps of the Anodizing Process:
1. Preparation:
The aluminum surface is thoroughly cleaned to remove any contaminants or grease that could interfere with the anodizing process.
2. Oxidation:
The aluminum is submerged in the electrolyte bath and subjected to direct current. The electric current triggers a chemical reaction that releases oxygen on the aluminum's surface, which bonds with the material to form the protective oxide layer.
3. Layer Thickness:
The thickness of the oxide layer can be controlled by adjusting the duration and intensity of the electrical current. Different applications require varying layer thicknesses, either for enhanced corrosion resistance or decorative purposes.
4. Coloring (Optional):
During or after the anodizing process, the porous oxide layer can be dyed. Special dyes are used to penetrate the porous structure and bind to the oxide layer, resulting in long-lasting color.
5. Sealing:
Finally, the anodized surface is sealed using hot water or steam, which closes the pores of the oxide layer. This step enhances resistance to external influences and ensures a uniform, durable surface.
Benefits of the Process:
Anodizing is an effective method to increase aluminum's resistance to corrosion, wear, and mechanical stress. It also offers extensive design options through optional surface coloring, making it ideal for both functional and aesthetic applications.
What colors can be achieved when anodizing aluminum?
A wide range of colors can be achieved through anodizing, including black, bronze, gold, blue, green, red, as well as colorless (natural silver/gray) and matte finishes. Custom color requests can be discussed and tailored to individual needs.
These colors are created by introducing dyes into the porous oxide layer during or after the anodizing process, resulting in long-lasting and UV-resistant hues.
Which aluminum parts can be anodized?
We process front panels, sheets, profiles, tubes, and small aluminum parts. Special requirements, such as anodized aluminum with a stainless steel appearance, are also possible.
The anodizing process can be applied to a wide range of aluminum components, ensuring durability, corrosion resistance, and aesthetic customization to meet specific design and functional needs.
Is it possible to anodize aluminum sheets in black or other colors?
Yes, we can anodize aluminum sheets in black, bronze, gold, white, and various other colors. The color is achieved through the choice of electrolyte and subsequent dyeing processes.
This allows for a durable, UV-resistant finish that enhances both the functionality and aesthetics of the aluminum sheets.
What advantages does anodizing offer compared to powder coating?
Anodizing has several advantages over powder coating:
Preservation of Natural Metal Appearance:
Anodized surfaces retain the metallic look of aluminum, making them ideal for designs requiring a sleek, natural aesthetic.
Higher Temperature Resistance:
Anodized layers withstand higher temperatures without degradation, making them suitable for applications in extreme environments.
Superior Abrasion Resistance:
The anodized oxide layer is harder and more wear-resistant than powder coatings, ensuring greater durability over time.
Precision Layer Thickness:
The thickness of the anodized layer can be precisely controlled, which is critical for technical applications requiring tight tolerances and dimensional accuracy.
These qualities make anodizing a preferred choice for industries that prioritize durability, aesthetics, and precision.
Which aluminum alloys are suitable for anodizing?
We work with alloys such as EN AW 6060, EN AW 7075, AlMgSi0.5, AlCuMgPb, and many others. Our experts are happy to advise you on whether your specific alloy is suitable for anodizing.
Each alloy reacts differently to the anodizing process, influencing properties like color uniformity, surface quality, and corrosion resistance.
Can stainless steel or other metals be anodized?
Classic anodizing is only suitable for aluminum and certain aluminum alloys. For stainless steel, we offer alternative surface finishing options.
These alternatives include processes like electrochemical polishing, passivation, or specialized coatings to achieve desired surface properties and aesthetics.
How thick is a typical anodized layer?
The layer thickness typically ranges between 10 and 25 micrometers, depending on the application. For technical applications, such as hard anodizing, thicker layers of up to 100 micrometers are possible.
The thickness is adjusted to suit the specific requirements, balancing durability, corrosion resistance, and functional needs.
What does E6/EV1 mean in anodizing?
E6/EV1 refers to colorless anodized aluminum with a specific surface quality.
E6 indicates a pre-treatment process, often mechanical or chemical, to achieve a fine, uniform surface finish before anodizing.
EV1 denotes the natural, silver-colored finish of the anodized aluminum.
This combination is widely used in architecture and construction for its sleek appearance and durability.
Can you produce gold or brass-colored anodized surfaces?
Yes, we offer anodized aluminum with gold or brass finishes. These surfaces are especially popular for decorative applications and provide a luxurious and durable appearance.
What is the difference between anodizing and eloxieren?
Anodizing is the English term for Eloxieren. Both terms describe the same surface treatment process for aluminum.
The process involves creating a durable oxide layer on the aluminum surface through electrochemical oxidation to enhance its resistance and appearance.
Can you anodize colored aluminum that is food-safe?
Yes, we provide food-safe anodized coatings, suitable for applications such as kitchen utensils, cookware, and packaging.
These coatings comply with food safety regulations, ensuring both durability and safe contact with food.